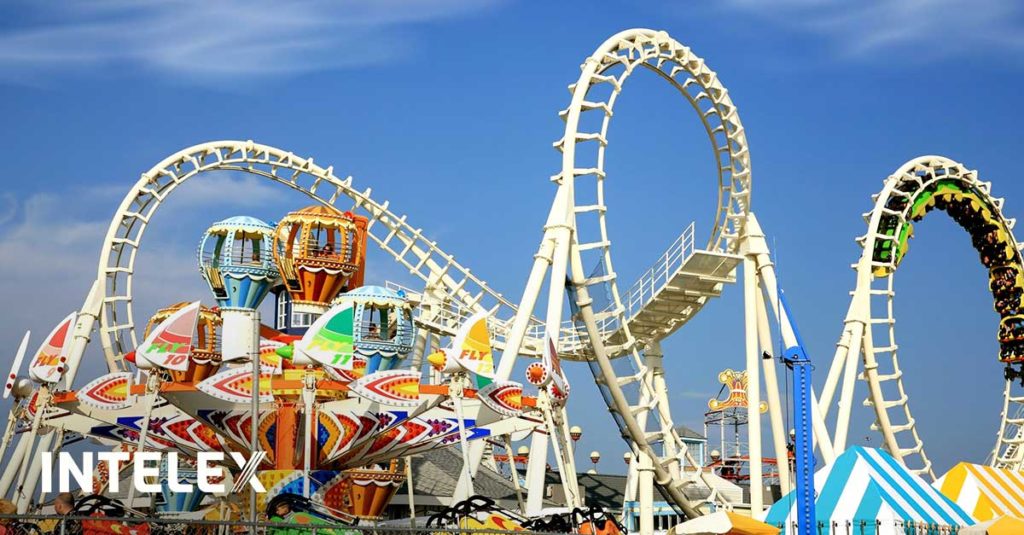
Roller coasters, ferris wheels, dodge ‘em cars, scramblers and rotors: Some of our greatest childhood (and adult) memories revolve around amusement parks and carnivals. However, it’s important to remember that fun can be serious business.
I realized that at a young age, when my father and I became stuck at the top of the double ferris wheel at the Ohio State Fair when I was five. The ride jammed for what seemed like hours; at this point, I don’t know if it actually was hours or 15 minutes. The event left an indelible mark on my brain and to this day, my palms start to sweat and itch when I think about riding on a ferris wheel.
As amusement parks and carnivals have reopened this year following universal shutdowns during most of 2020 and early 2021, many families rushed to take advantage of the summer fun that was denied them in 2020.
However, some high-profile incidents highlight the need for safe operations. In 2019, the last year for which statistics are available, approximately 385 million guests enjoyed 1.7 billion rides at 410 fixed sites in North America. That number doesn’t include local and state carnivals that don’t operate from fixed sites.
According to the 2019 Ride Incident Survey Report, the chance of being seriously injured on a fixed-site ride at a U.S. amusement park is one in 15.5 million rides taken. That doesn’t seem like a high number, but it translates to 1,299 ride-related injuries in 2019.
A water park in Spring, Texas, was evacuated on July 17, 2021 when a chemical leak resulted in 29 people being taken to area hospitals, and nearly 40 others declined further medical care following decontamination procedures. Some of those exposed to the chemical fumes, which included bleach and sulfuric acid, were children and one was hospitalized in stable condition.
“We are working hand in hand with Harris County Public Health officials, along with third party industry experts, to determine a cause, and we will reopen when we are confident it is safe to do so,” said Jeff Filicko, a spokesman for the park, in a statement.
Houston’s chief elected official, Lina Hidalgo, head of Harris County’s governing body, the Harris County Commissioners Court, tweeted that she was grateful for the swift action from first responders at Splashtown, and added, “We’ve issued a closure order to investigate and ensure the park meets all requirements before reopening again.”
In Ohio, lawmakers passed HB 189 in 2019, commonly known as “Tyler’s Law,” which was named after high school student Tyler Jarrell, who was killed in 2017 when part of a ride at the Ohio State Fair broke off and flung four people to the ground, killing him and injuring the three people who were on the ride and one person on the ground. It was determined that a steel arm that was part of the ride was corroded and had snapped off. The ride owner claimed the ride had been inspected just hours before the incident, and attorneys for the victims say state inspectors failed to see signs the ride was no longer safe.
Like any production equipment and process systems, the equipment at amusements parks is subject to equipment failure, chemical releases, operator errors and all of the other risk factors that can contribute to fatalities and injuries as well as a production slowdown or stop.
“This equipment is subject to significant physical stress every day, and seemingly minor issues like rust or external corrosion could be leading indicators for more significant problems that are aggregating under the surface. Everything can look fine right up until it isn’t, and that can happen very suddenly,” said Graham Freeman, a subject matter expert on quality and management systems for Intelex Technologies.
Tyler’s Law Requires Reviews and Inspections of Rides
On November 6, 2020, rules adopted pursuant to HB 189, more commonly referred to as Tyler’s Law, went into effect. The Ohio Department of Agriculture adopted these rules to establish increased safety measures for amusement rides. The rules adopt new ASTM standards, collect information regarding the storage or use of rides outside of Ohio and specify the frequency of inspections and number of inspectors who will perform those inspections.
The law categorizes rides and establishes protocols for ride owners to complete fatigue and corrosion reviews and inspections, based on category of ride. The categories are as follows:
- “Low Intensity Rides”: All kiddie rides, carousels, go karts, and inflatable devices. For the purpose of this rule, kiddie rides are all rides that are primarily designed for children 48 inches and under.
- “Intermediate Rides”: All rides that are not classified as low intensity rides, towers, or roller coasters pursuant to this rule.
- “Towers”: Any amusement ride, other than a roller coaster, whose main body components exceed twenty feet in height.
- “Roller Coasters”: Any ride licensed as a roller coaster pursuant to section 1711.53 of the Revised Code and whose main body components exceed fifty feet in height.
Owners of intermediate rides, towers, and roller coasters were required to complete the following as of April 1, 2021:
- Ensure all rides meet the manufacturer’s minimum requirements for inspection and testing.
- Annually perform a complete visual inspection of a ride’s structure including removing access panels where possible to do so. Special attention shall be given to structural members and their connections for signs of fatigue or corrosion.
- If fatigue or corrosion are found, the owner will discuss the findings with the ride’s manufacturer and implement mitigation strategies.
According to Freeman, including the manufacturer in the inspection process “is an excellent way to make sure their quality management expertise is brought to bear on the condition of the equipment. They know the equipment better than anyone, and they can identify right away if deviations are being normalized in favor of efficiency and profit. It also means that inspections can be logged in the manufacturer’s digital QMS, which is critical for creating a record of nonconformances and scheduling future inspections.”
For orphaned amusement rides, the owner shall seek the consultation of a registered professional engineer in good standing. If fatigue or corrosion are found, the owner will discuss the findings and implement mitigation strategies as recommended by the registered professional engineer.
Documentation of the visual inspection and the findings shall be made available to ODA for review. Additionally, the documentation shall be maintained for the life of the ride and transferred to any subsequent owner. The ride owner shall ensure compliance with the mitigation strategies, if any, pursuant to the recommendations made by either the manufacturer or registered professional engineer where applicable.
Inspectors across Ohio are conducting mandatory checks for rust and metal fatigue and, according to an article published by Industrial Equipment News, “increasingly flagging rides for repairs during the first year of enforcement under the new regulations.”
According to the article, some carnival operators complain inspectors are overreaching and shutting rides “over issues that aren’t immediate safety concerns.” David Miran, who heads Ohio’s amusement ride safety office, told IEN that the law emphasizes checking a ride’s structural components and that inspectors are told to err on the side of caution.
Surprisingly, nine states don’t require any government inspections of amusement park rides.
Intelex offers a variety of software solutions related to risk management, tracking nonconformances and scheduling future inspections, such as Inspection Management Software, Root Cause Analysis Software and CAPA Software, to name a few.