Kamerasystem Kameragestützte Montagehilfe: So überprüft ein Roboter bei Miele Bauteile
Beim Hausgerätehersteller Miele automatisiert ein Kuka Roboter die Produktion von Antriebsmotoren für Wäschetrockner. Mit Kamerasystem am Greifer prüft der Roboter Bauteile, positioniert – und arbeitet dabei auch noch weitgehend eigenständig.
Anbieter zum Thema
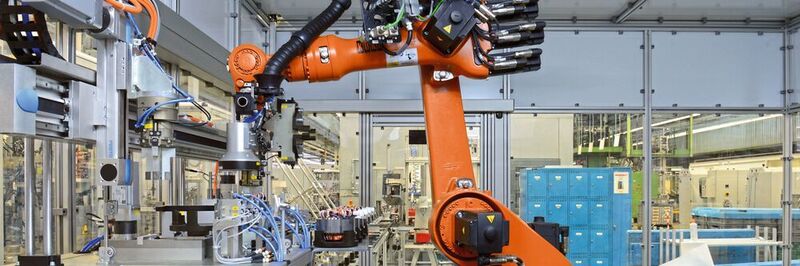
Roboter arbeiten zunehmend autonom. Ein Grund dafür: Kamerasysteme nehmen immer präziser ihre Umgebung wahr. Damit können sie auf veränderte Situationen flexibel reagieren und Stillstandzeiten deutlich reduziert werden. Ein Beispiel dafür findet sich in der Produktion des Hausgeräteherstellers Miele. Dort führt ein Kuka Roboter der niedrigen Traglastklasse kameragestützt Bauteile dem Montageprozess zu.
Mit Sensoren oder Kamerasystemen nehmen Roboter ihre Umgebung immer präziser wahr. Dadurch können sie flexibel auf neue Situationen reagieren, und es entstehen völlig neue Anwendungsmöglichkeiten. Die Vorteile für die Unternehmen liegen auf der Hand: mehr Autonomie der Industrieroboter, mehr Flexibilität im Bauteile-Handling und kürzere Stillstandzeiten.
Die beiden Unternehmen Heinen Automation und ID Ingenieure & Dienstleistungen sind auf die Umsetzung von roboterbasierten Applikationen spezialisiert. Gemeinsam haben sie ein Palettier-System beim Hausgerätehersteller Miele & Cie. KG im Werk in Euskirchen in Nordrhein-Westfalen geplant und umgesetzt. Ein Kuka Roboter führt dabei kameragestützt Bauteile der Produktion zu. „Es war der explizite Wunsch von Miele, eine individuelle Handlings-Applikation zu realisieren, die einfach und schnell auf unterschiedliche Bauteile und Montageprozesse umgestellt werden kann“, sagt Michael Miessen, verantwortlich für das technologische Konzept der Anlage bei der Heinen Automation GmbH & Co. KG.
Roboter punktet gegenüber Linearportal
Das Palettier-System muss unterschiedliche Bauteile bearbeiten können. Deshalb entschieden sich die beiden Unternehmen für die roboterbasierte Applikation, denn diese bietet gegenüber einem manuellen Prozess oder einem Linearportal mehrere Vorteile. „Insbesondere unter ergonomischen Gesichtspunkten war die manuelle Tätigkeit nicht mehr zeitgemäß. Dazu kommt, dass die Taktzeiten erhöht werden sollten, was in der bestehenden Form nicht mehr möglich war“, erklärt Michael Gottschalk, Geschäftsführer der ID Ingenieure & Dienstleistungen GmbH, die Aspekte für einen Roboter. „Um Platz zu sparen, die Anlage wirtschaftlich umsetzen und um die nötige Flexibilität gewährleisten zu können, wurde auf eine aufwendige Zellenkonstruktion verzichtet.“
Im Mittelpunkt der Anlage steht ein Kuka Roboter vom Typ KR 20. Das Besondere: Er ist am Greifer mit einer Kamera ausgestattet. Diese prüft sowohl die Menge der zu bearbeitenden Bauteile sowie deren exakte Position. Und sie erkennt Fehler, die durch den Transport oder durch menschliche Eingriffe entstanden sind. Damit ist die roboterbasierte Applikation äußerst flexibel und verfügt über einen hohen Grad an Autonomie.
Vorab-Kontrolle: Kamera erkennt Position und Fehlteile
„Die Aufgabe des Roboters besteht darin, teilgeordnete Statoren automatisiert dem Montageprozess zuzuführen“, sagt Michael Miessen. Die unbeweglichen Motorenteile sind Teil des Antriebsmotors der Haushaltswäschetrockner. Im ersten Produktionsschritt liefert ein Mitarbeiter die Paletten mit Kleinladungsträgern (KLT), in denen die Statoren lagern, mittels Hubwagen an die Anlage an und legt sie auf dem Aufnahmerollgang ab.
Nachdem die Palette in den Arbeitsbereich des Roboters zugeführt wurde, verfährt der Roboterarm darüber. An einem seiner Mehrfachgreifer ist eine Kamera angebracht, die die Befüllung der Kleinladungsträger prüft. Anschließend bewegt sich der Roboter über den ersten zu packenden Stator und prüft dessen genaue Positionierung.
Die Prüfung ist notwendig, da die Bauteile aufgrund von Erschütterungen beim Transport oder durch Verschleiß des KLT mehrere Zentimeter von der Norm abweichen können. Mithilfe der Kamera können die Abweichungen erkannt und die Statoren ohne Hilfe des Werkers autonom mit dem Robotergreifer aufgenommen werden.
Anschließend legt der Roboter das Bauteil in einer Wendestation ab. Dort wird dessen exakte horizontale Lage in der Ausgangsposition und nach einer 180°-Drehung bestimmt. Das ist notwendig, um eventuelle Unebenheiten im Hallenboden auszugleichen. An diesem Punkt endet die Arbeit des KR 20 an dem Bauteil. Die weitere Bearbeitung übernimmt ein Handling-Portal, das den Stator schließlich im Warenträger positioniert.
Der Roboter wiederholt währenddessen den Arbeitsvorgang so lange, bis der Kleinladungsträger geleert ist. Diesen stapelt der Roboter der niedrigen Traglastklasse anschließend auf einer Palette auf dem Entnahmerollgang.
Sind alle KLT entleert gestapelt, wird die so befüllte Palette aus der Anlage transportiert. Der gesamte Prozess kommt somit ohne Eingreifen eines Werkers aus.
„Wir freuen uns, dass wir ein wirtschaftliches, aber auch flexibles und platzsparendes Anlagendesign geschaffen haben. Vor allem, dass der Roboter in der Lage ist, mit verschiedenen Statoren aus einem Verpackungsbehälter umzugehen, ist ein großes Plus an Flexibilität“, sagt Michael Gottschalk. Schließlich muss der Roboter an 220 Tagen im Jahr durchgehend im Zweischichtbetrieb die Statoren zuverlässig anliefern.
Die Verfügbarkeit sollte laut Miele 95 % betragen. Zudem sollte eine Autonomiezeit von 104 min gewährleistet sein. Das entspricht bei drei vollbeladenen Paletten mit je 160 Statoren einer Taktzeit von 13 s. Weitere Kuka Komponenten sind die Steuerung KR C4 sowie die Profinet-Schnittstelle. Die Anlage ist seit Anfang März 2018 in Betrieb. „Wir freuen uns, dass die Umsetzung so reibungslos geklappt hat. Bislang erfüllt die Anlage zu 100 % unsere Erwartungen“, kommentiert Jürgen Zdunek, Fertigungsleiter bei Miele in Euskirchen.
* Sebastian Schuster, Global PR & Content Manager bei Kuka
(ID:45815032)