EMMETSBURG, Iowa—The Project Liberty plant is a multi–$100-million effortto get ethanol for cars past the obstacles of food-versus-fuel debates, farmer recalcitrance and, ultimately, fossil fuels. It is also the fruition of a 16-year journey for founder and executive chairman Jeff Broin of ethanol-producing company POET—an odyssey that began with a pilot plant in Scotland,S.D., and progressed througha grant of $105 million from taxpayers via the U.S. Department of Energy (DoE).
The government invested because of hopes that such advanced biofuels could reduce global warming pollution from vehicles compared with gasoline. And making ethanol from inedible parts of corn plants is perhaps better than using the edible starch in corn kernels that could find use as food or feed for animals. “We’re processing about 770 tons a day of corn stover—basically the leftovers from the cornfield—into ethanol,” Broin told me during a tour of POET’s new Project Liberty facility, which makes ethanol from cellulose and is located next to a traditional facility that produces the fuel from the starch in corn kernels. “[It’s] one of the first plants in the world to do that, so we’re pretty excited.”
.jpg?w=250)
Project Liberty Credit: © David Biello
On supporting science journalism
If you're enjoying this article, consider supporting our award-winning journalism by subscribing. By purchasing a subscription you are helping to ensure the future of impactful stories about the discoveries and ideas shaping our world today.
The ability to make fuel from corn stover is the result of nearly two years of tinkering since the plant officially opened in September 2014. And Project Liberty is one of the culminations of an American effort to break oil’s monopoly on transportation fuels in favor of domestically grown biofuels. Most recently, the U.S. Congress mandated that a certain percentage of the fuels used in U.S. vehicles come from biofuels under the terms of the Renewable Fuel Standard federal program, which came into effect in 2005 and mandates the development of biofuels. The RFS put a particular focus on biofuels that do not come from food, as traditional corn ethanol comes from starch that can serve as food or animal feed. The great hope was for cleaner, greener ethanol to be made from cellulose, the inedible plant fiber in the corn leaves, stalks, husks and cobs.
Getting Project Liberty up and running has already required an investment of at least $275 million from POET and its Dutch partner Royal DSM, including grants from the DoEand the state of Iowa. Assuming the kinks are now ironed out, the plant could use some 260,000 metric tons of the nonedible parts of corn plants to produce as much as 95 million liters of cellulosic ethanol each year. Already bales of stover sprawl around the new facility, waiting to be consumed by an industrial process—instead of by mushrooms.
.jpg?w=225)
Shredded stover Credit: © David Biello
Project Liberty basically industrializes what fungi growth and other decay processes accomplish naturally to release the solar energy stored up by green plants. The corn stover is first freed from its baling and shredded.
The strips of corn leaves and chunks of corncob are then bathed in sulfuric acid to begin breaking them down into fibers. Enzymes—biological proteins freed from their living hosts to do industrial work—eat into those fibers further, and the resulting sour soup is processed to remove water.
This mash, which looks like mud, then goes into giant fermentation vats where specialty yeast eats the sugars in it to produce ethanol.

Cellulosic ethanol feedstock "mud" Credit: © David Biello
At this point, the mud still contains leftover fibers, particularly lignin—the tough strands that allow cornstalks or trees to stand tall and resist decay while living—which becomes an industrial fuel for the facility’s boiler after being pressed into coal-like cakes.
And the rest of the leftovers are fed into one of the nation’s largestbiodigesters—reactors that can hold some four million liters of leftovers for anaerobic digestion—to make methane that the plant can use for power, eliminating its need for natural gas fuel. This helps reduce greenhouse gas pollution, as does the facility’s main product—a fuel fermented from plant material that pulled carbon dioxide out of the sky while growing. Burning cellulosic ethanol as a fuel could result in just 10 percent of the CO2 emissions produced by burning gasoline.

Corn products Credit: © David Biello
One big secret to making it all work is the advanced biofuel refinery's location right next to a conventional corn ethanol plant, which makes ethanol from the starch in corn kernels. That facility is roughly half the size of its cellulosic fuel neighbor, costs less than half as much to build and run, and produces twice as much ethanol. It can use the leftover lignin and biodigested methane from the cellulosic facility as fuel for distillation and other processes. "We literally can shut off the natural gas valve to the starch plant," Broin notes.
There are plenty of cellulosic leftovers on farm fields and elsewhere in the U.S., not just corn stover but also from other energy crops such as switchgrass, along with wood waste and agricultural remains such as wheat straw. The DoE estimates that roughly 900 million metric tons of such material is available each year—a renewable resource that could make about 300 billion liters of ethanol. And there are plenty of conventional ethanol plants near which to locate—almost 200 according to the most recent data from DoE—and that is just in the U.S. "We see the opportunity to build these plants all over the world," Broin says.

Stacked stover outside Project Liberty Credit: © David Biello
POET is not alone. Agrochemical giant DuPont opened its own cellulosic biorefinery next to a conventional starch-based fuel facility last October in Nevada, Iowa, and it should eventually be able to produce around 115 million liters of cellulosic ethanol per year. “You know, it’s been a long time coming but we’re proud it’s here,” Terry Branstad, governor of Iowa, said on October 30 last year at the opening of the new DuPont facility, which is still not running at capacity.
“Thirty million gallons of biofuel will be produced without consuming a single additional bushel of corn,” added U.S. Sen. Chuck Grassley, a longtime ethanol supporter and one of the architects of the RFS. “You have achieved here what Congress hoped: new biofuels that were cleaner, greener and more efficient.”

DuPont's cellulosic ethanol biorefinery in Iowa Credit: Courtesy of DuPont
But the opening of DuPont’s new facility also occasioned the shutdown of DuPont’s other cellulosic refinery in Tennessee. “DuPont remains committed to the commercialization of cellulosic biofuel and will focus its resources on its Iowa facility,” Jan Koninckx, DuPont’s global business director for advanced biofuels, told Scientific American in an e-mailed statement.
Cellulosic fuels’ main hurdle seems to be economic. In April 2012 Blue Sugars Corp. of South Dakota produced the first batch of qualifying cellulosic ethanol, a little more than 75,500 liters, then promptly went out of business. In 2013 no cellulosic ethanol was produced but by last year—after several DoE-supported plants came online—all five of those biorefineries produced a total of 8.3 million liters of cellulosic ethanol, according to the U.S. Environmental Protection Agency, which administers the RFS. Already, Spanish multinational corporation Abengoa’s cellulosic ethanol plant—which opened in 2014 in Hugoton, Kans.—sits unused due to technology troubles as well as Abengoa’s bankruptcy. That plant consumed a $132-million loan guarantee as well as a $97-million grant from the DoE before idling.

Abengoa's shuttered cellulosic plant in Kansas Credit: © Bill Kubota
Simply put, cellulosic ethanol is more expensive to make than ethanol fermented from cornstarch or from sugarcane, the world’s second-largest source of fuel ethanol. “Everything’s expensive here because it’s first of a kind,” Broin says. “The next plant will be a lot cheaper.”
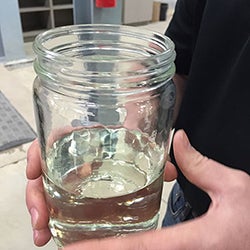
Cellulosic ethanol: it smells much worse than it looks Credit: © David Biello
On a more basic level, moving fibers and sludge through an industrial facility is tough to do without breakdowns. The corn stover arriving at POET’s cellulosic facility had as much as three or four times more sand and gravel mixed in than engineers had anticipated, and that grit wreaked havoc on pumps, valves and other equipment.
“We have made literally hundreds of small process changes,” including a thorough washing of the corn stover once it comes out of the bale, Broin says. There have also been not-so-small process changes, such as using large cranes to tear open buildings in order to replace equipment.

Corn stover up close Credit: © David Biello
But Broin notes that ethanol from corn faced the same difficulties during its ascent over several decades. And cellulosic ethanol is now definitely being produced in meaningful quantities at Project Liberty. “We're shipping cellulosic ethanol,” Broin says. “We’re filling railcars.”
That's good because the EPA now requires nearly 1.2 billion liters of cellulosic biofuels in 2017 under the terms of the RFS. That's still well below where lawmakers like Grassley thought cellulosic ethanol would be by now—they had established a target of some 11 billion liters per year back in 2007. When that failed to materialize, the EPA mandated at least 465 million liters of cellulosic biofuel in 2015, but only saw 8.3 million liters mixed into the nation's fuel supply. So the rest of the nearly 57 billion liters of ethanol fuel came from corn kernels, with attendant concernsabout industrial farming practices, water pollution and impacts on food prices.

Flex fuel future? Credit: © David Biello
“Everything about ethanol is good, there is nothing bad. It’s good for agriculture, good for the environment, good for economic development in rural communities,” Grassley told Scientific American at the DuPont opening in October. “We will demonstrate that we can produce food and fuel forever. We don’t need to worry about choosing between food and fuel.”
The combination of cellulosic biorefineries with starch-based ethanol plants could prove more potent economically, but it fails if the goal is to reduce the amount of ethanol made from corn. Instead of replacing corn ethanol, cellulosic ethanol may simply supplement it.

Ethanol from corn kernels, lots and lots of corn kernels Credit: © David Biello
Regardless, the ethanol industry’s ambitions are much larger than just Project Liberty and its peers or even the hundreds of conventional ethanol fuel plants: The sector hopes to one day produce around 570 billion liters a year, including a major contribution from cellulose, according to Broin. “There’s a big market out there that we’d like to replace—that’s the entire gasoline market,” Broin says. “We can grow our way easily out of our reliance on fossil fuels and people just don’t understand that.”
To learn more about ethanol—cellulosic and otherwise—tune in this fall to The Ethanol Effect on PBS, hosted by David Biello.